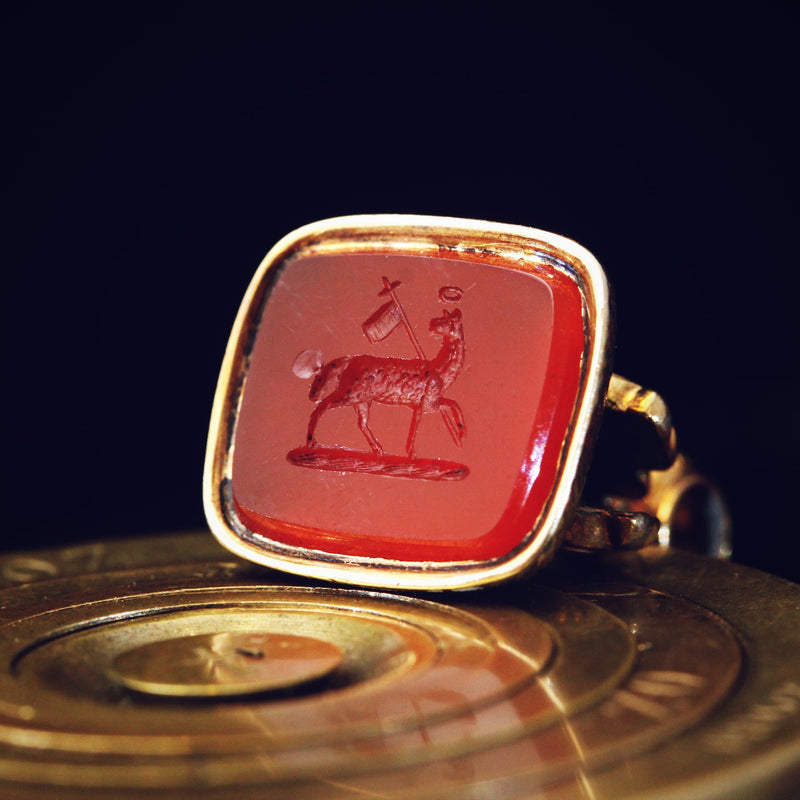
Intaglio is the art of carving a design or crest into precious metal or a suitable gemstone, so that all the design remains below the surface. It is the opposite of a ‘relief’ sculpture such as a Cameo, and is carved into metal, precious and semi-precious stones, which produce a positive imprint when pressed into a soft material such as heated sealing wax upon a letter or document.

Intaglio have been used as seals in this manner since antiquity and these objects were highly prized amongst many cultures, being traced right back to the Sumerian period in Mesopotamia.

An engraved gemstone was a valued possession and would only have belonged to someone of great wealth and importance, but in early times due to the limitations of tools it was only possible to carve into relatively soft stone, making it extremely difficult to produce a detailed and durable image.
In Europe, the history of gem engraving can be traced back to Greece in the second quarter of the 6th century BC. These carved gemstones were much valued and sought after by the wealthy Greeks and the evolution of new methods to carve harder and more durable stones and gems can be seen at this time. These include the carvers using a cutting wheel and a drill, probably powered by a bow, whereas before the carvings had been gouged freehand into the soft stone.

These techniques passed to the Romans who improved the basic tools and with the use of drills and wheel technology facilitated the production of more intricate and detailed images. An extremely finely carved seal made forgery difficult, which was of utmost importance in Roman society, as an intaglio seal stone, often mounted in a ring was used by its owner to validate official documents.
The Roman intaglios differed little from the earlier Greek ones and were cut into a variety of stones such as Garnet, Carnelian and Amethyst. The gemstones were cut using abrasive powder from harder materials such as emery. Emery was mined on the Greek island of Naxos until recent times, and consists of low grades of the mineral Corundum, mixed with other minerals such as Spinel. The Romans are considered to have mastered the high art of Intaglio carving and there are many excellent examples surviving today in museums.

This specialised art of intaglio gem engraving was slowly lost along with the fall of the Roman Empire but there were major revivals in Europe during the Middle Ages and the Renaissance period including in 15th century Italy where there was a revival in the art of gem engraving as a result of interest in and admiration of Classical culture with many pieces of intaglio jewellery being unearthed from ancient Roman sites. By this time intaglio seals had lost all but their original purpose but this interest in collecting in turn led to a new school of gem engravers keen to re-learn the art which had been lost for centuries to supply the market with new intaglio items in the style of the ancient Roman ones.

During the Neo Classical Revival in the 18th century, connoisseurs feverishly collected intaglio from the ancient and earlier periods, often re-setting them in contemporary jewels. Because of their scarcity demand by affluent Europeans to acquire these carved gems outstripped supply and so led to a further re-invigoration of the art. Copies were made of the classical designs by the most skilled engravers of the time and by 1800 there were engraving studios in Italy, France, Germany and England.

Of note was Lorenz Natter (1705 – 1763) a well-travelled 18th century gem engraver who published A Treatise on the Ancient Method of Engraving on Precious Stones compared with the Modern. It was published in London in 1754. Natter was one of the foremost exponents of the art in the first half of the 18th century and in the publication he explains his techniques; the size of the tools used gradually decrease from that of a large pea to the fine point of a needle. He says; ”one puts on the head of the tool some diamond powder moistened with philosopher-oil (linseed oil and powdered brick), which is the most thinnest and fixest than other oils. Then turning the great wheel with the foot, the stone (which is cemented with mastic to the end of a little stick) is applied to the tool to be engraved, the figure having first drawn on it with the point of brass or diamond.” This description is very similar to the tools and techniques used by the Romans 1000 years earlier.

Intaglios have remained greatly prized and collected by today’s connoisseurs and most of those we have in our collections date to the 19th century and can be found in the form of fob watch seals showing family crests, mottos and monograms. We can arrange for items to be engraved and although it could be considered pricey, (Helen paid £300 for her family crest on her signet ring) we feel that the expense very much justifies the result as one then has a completely personal heirloom as a talisman and to carry your family story forward.
These days there are three methods used for intaglio engraving; hand, rotary machine and laser.

Hand Engraving
This is the oldest and most labour-intensive method and is performed by a very skilled engraver using a small engraving tool. The result may not be quite as exact as a computer-controlled engraving, but it is much prized because of the value of the craftsmanship and of course, it is the most expensive as it is so time consuming.
Rotary Machine Engraving
In this method a tool is controlled by a machine to make the engraving. The design is programmed into a computer which controls the machine, making the engraving very precise. This method takes less time and is more affordable but cannot be used on materials that are heat sensitive. The friction causes heat, which can potentially damage some jewellery.
Laser Engraving
This is the most modern and adaptable method. A computer-guided, highly concentrated laser beam performs the engraving. The thickness of the beam can be adjusted to change the width of the engraving, and the laser power can also be increased to carve more deeply into the base material.
Intaglio Collections in Museums
Links to companies who offer Intaglio engraving;