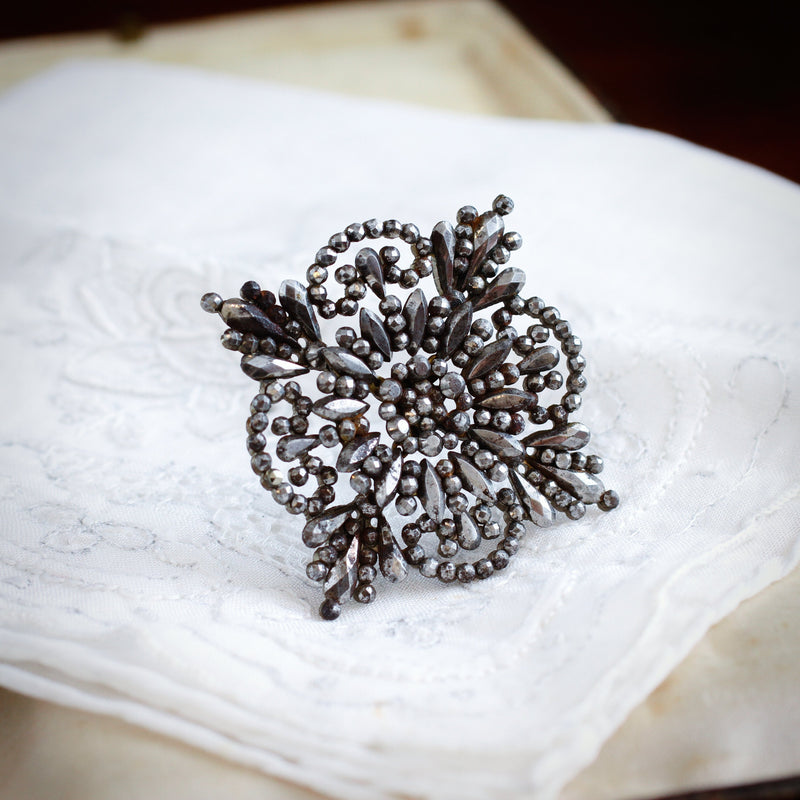

The making of Cut Steel accessories and jewellery originated in England in the 17th century. It is believed that the technique of 'ornamental steelwork' first developed in the town of Woodstock in Oxfordshire, as this industry which was well established by 1720 became famous for 'the finest, most elaborate and expensive workmanship in steel toys'; acoutrements or accessories as we might now call them including shoe buckles, watch chains and keys, buttons etc, and included making 'stars' for the chivalrous orders.(1). The trade also grew in both Clerkenwell in London and amongst the steelworkers in Wolverhampton.

Steel, when polished can take a high shine, greyer than silver but highly reflective and very attractive. These Steely 'stones' became very fashionable and were used to adorn buttons, buckles, hair ornaments, and all manner of jewels as this famous antique print from the period shows, they could be quite bright!! (2). They were a more affordable alternative to Diamonds and were worn by both men and women alike. 'Popular from 1700’s through to Victorian times and a little beyond, cut steel is best described as a ‘mushroom’ of steel, the top of which is faceted and polished to a very high shine. Each ornately cut and individually polished stone then has individual facets. The more facets each ‘stone’ has, and the more tightly packed together they are, the better quality the item'. (3).

In the early days the technique of decorative 'cut steel' involved cutting and hand faceting small steel studs into various shapes (as you would a gemstone) and riveting them (as the making of Steel jewellery comes from a metal-working rather than a jewellery-making origin) onto a backplate which was cut to the desired design. Apparently it could take as long as two weeks for a single person to make a pair of buckles (4). The pieces would be made from the purest or best steel that could be afforded, from which the studs were then cut into the different shapes. These shapes have particular names; the most common shape is the round faceted stud in various sizes, but there is also the frustra, a flattened or truncated cone shape; the vesica, what we would now call marquise or navette shaped; and faceted oblong bars and crescent shapes too. This brooch in our shop has several of these shapes. These early entirely handmade pieces can be distinguished from the later by the variety of shapes, the small size and greater number of facets to each stud.
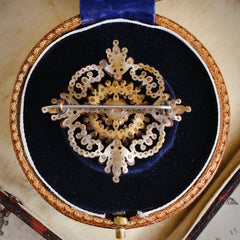
At the height of the fashion for shoe buckles in the 1770's, George III appointed John Worralow of Wolverhampton as the Royal Steel Buckle maker. This gentleman soon came to make pieces, including buttons, chatelaines etc. for the royalty in Spain, France and Russia and his work which was of the utmost quality was not cheap. At this time pieces did begin the be produced in France by some entrepreneurial Englishmen who set up workshops in Paris, but the main centres were still in England. George Wallis, one of the great Victorian art gurus, was born in Wolverhampton in 1811, and writes about the trade in steel ornaments; 'Let them remember that 100 years ago [sc. c. 1760] a large trade existed with France and Spain in the fine steel goods of Birmingham and Wolverhampton, of which the latter were always allowed to be the best both in taste and workmanship. A century ago French and Spanish merchants had their houses and agencies at Birmingham for the purchase of the steel goods of Wolverhampton. These fine steel ornaments, chains, chatelaines, sword handles, &c., were often purchased at their weight in coined gold - Spanish Dubloons in one scale, steel goods in the other! Single chains, by first class makers, would fetch 25 guineas. The beaus and belles of the French and Spanish courts glittered on state occasions in the steel ornaments of the little Staffordshire town, the skill of whose artisans made made native iron glisten like diamonds' (5).
Another famous maker was Matthew Boulton, who had workshops in London and Birmingham and produced pieces of the finest quality in his Soho factory in Birmingham. 'He inherited his ‘toymaking' business, which at that time meant producing both useful and decorative products in polished iron and steel, brass, copper and silver, from his father. By 1766 his factory at the Soho Works in Birmingham, with up to 600 employees in more than 60 workshops, was one of the most famous in Britain.' (6). This buckle is believed to have been made by Boulton as it combines both ormulu and cut steel and is in his Neo Classical style which was is distinctive to his output. He also notably worked alongside Josiah Wedgewood and produced beautiful pieces set with Wedgewood 'cameos'.
Eventually the craze for shoe buckles waned and by the 1820's although shoe ornaments were still made to be stitched onto the shoes, the trade had turned mostly to jewellery and other toys such as; buttons; buttonhook; beads for decorating clothing; chatelaines etc. Most of these later pieces are not of the same high quality as the earlier ones as by this time the techniques used had changed and pieces were stamped out rather than cut by hand as greater mechanisation had made possible faster production of these popular items. There are many pieces of exquisite cut steel work to be seen in museums and these pieces are a wonderful and inexpensive item to collect, although as they become recognised for the mini works of art they are prices may rise accordingly.
Further, more detailed information concerning the development of the industry can be found on the website of the Wolverhampton Museum, with some very informative articles written by Frank Sharman. The museum also which has a collection of antique pieces of both jewellery and 'toys'.
References
1. Clifford, Anne (1971). Cut-Steel and Berlin Iron Jewellery. Adams & Dart. pp. 13–14.
2. 'Coupe de Bouton' print. Lewis Walpole library.
4. Reinhold Angerstein, visited and wrote in his journal about the steel 'toy' making industry in Woodstock in 1753.
5. http://www.historywebsite.co.uk/Museum/metalware/steel.htm
George Wallis. Jewellery, 1878.